Planificación de Paradas - Parte 1: Definición de Alcance y Desarrollo del Cronograma
- Frontline
- 23 sept 2024
- 5 Min. de lectura
Actualizado: 27 nov 2024
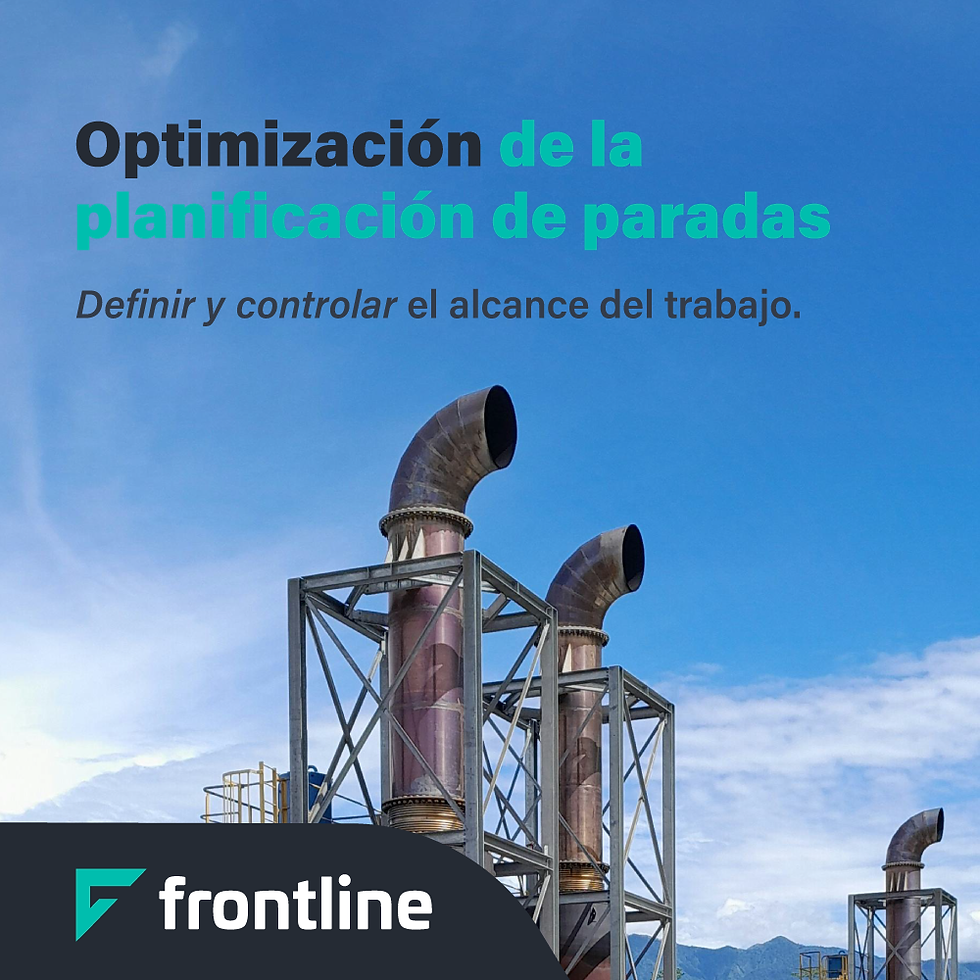
Esta es la primera parte de una serie de publicaciones sobre la planificación de paradas en plantas petroquímicas (turnaround/shutdown en inglés). El éxito o el fracaso de las paradas depende en gran medida del alcance del trabajo que se va a realizar y del control que tiene el equipo sobre su ejecución. Una adecuada definición del alcance del trabajo que se va a ejecutar durante la parada y controlarlo para evitar cambios de última hora sienta las bases para un proyecto exitoso.
Se requiere un proceso detallado, exhaustivo y colaborativo que involucre a los equipos de ingeniería, fiabilidad, operaciones y al equipo de paradas para definir el alcance del evento. En primer lugar, es necesario realizar una evaluación exhaustiva de la unidad o plantas, teniendo en cuenta el historial de mantenimiento, las necesidades operativas o las mejoras que se van a introducir. El resultado de esta evaluación pasa entonces al modo de definición, donde los equipos de planificación y ejecución de paradas/proyectos deben definir cómo ejecutar el trabajo. El objetivo principal es equilibrar el mantenimiento requerido con las mejoras que se van a realizar y, al mismo tiempo, evitar cambios, adiciones o inclusiones de última hora que puedan poner en peligro la parada.
Una vez que se conoce más o menos el alcance del proyecto, los planificadores deben empezar a definir la secuencia de tareas para entregar cada paquete de trabajo. Idealmente, este trabajo comienza 18-24 meses antes del evento. El principal desafío de la planificación de este tipo de proyectos es que el cronograma está compuesto por cientos, sino miles, de "pequeños" paquetes de trabajo individuales e independientes. El trabajo que se debe realizar en el intercambiador de calor numero 1 es muy similar al que se debe realizar en el intercambiador de calor número 100, pero cada uno debe ser examinado en detalle y luego ensamblado dentro de un cronograma de parada coherente. Hay que sumar numerosas disciplinas: equipos mecánicos, eléctricos, de instrumentación, tuberías, equipos rotativos, etc. Cada paquete individual de trabajo es relativamente fácil de planificar (aislar → descontaminar → abrir → reparar/mantener → inspeccionar → prueba hidráulica → reconectar); el enorme desafío radica en alinear los miles de paquetes en un solo plan.
Para desarrollar una primera versión del cronograma, los planificadores suelen mirar:
Cronogramas de paradas anteriores para la misma unidad (típicamente en P6/MSP, a veces incluso en Excel)
Planes de mantenimiento anteriores (típicamente en Excel)
Referencias o tablas de rendimiento (benchmarks) de la empresa o de la industria (si están disponibles)
Alcance a ser ejecutado en la parada
La forma más fácil de empezar a introducir la información en el cronograma es utilizar información de una parada anterior si se ha realizado el mismo trabajo, y si se ha seguido correctamente el progreso y si se ha definido correctamente en el cronograma. En tal caso, es “simplemente” una cuestión de copiar y pegar. Sin embargo, hay muchos "si" involucrados, y cualquiera que haya utilizado software de planificación de proyectos como P6 o MSP sabe que la funcionalidad de "copiar y pegar" de Excel/Word puede ser bastante laboriosa en estos software de planificación de proyectos. La descripción de la actividad, el código de actividad, la ubicación y la estructura de la WBS, los recursos, los calendarios, etc., variarán de una parada a otra y deben actualizarse manualmente.
Un simple “copia y pega” del trabajo realizado en una válvula de seguridad de un cronograma de parada anterior al nuevo cronograma podría llevar de 15 a 30 minutos. Esto solo es posible si toda la información del cronograma anterior es correcta (secuencia y duraciones) y se identifica fácilmente.
Suponiendo de forma conservadora que hay 1000 unidades de trabajo para una parada, y que todas están correctamente registradas en los cronogramas de paradas anteriores, un planificador tardaría 3,5 meses en desarrollar el nuevo cronograma de paradas, simplemente "copiando y pegando".
1000 unidades 30 min/unidad = 30,000 minutos / (60 min 40 h por semana) → 12.5 semanas
Esta situación rara vez se da y, desafortunadamente, lleva mucho más tiempo desarrollar una primera versión de un cronograma. Esto se debe a numerosos motivos:
No todas las paradas tienen el mismo alcance, algunos equipos se abren cada 2-3 ciclos de parada (8 o 12 años)
La estructura y la lógica del cronograma rara vez se mantienen de un ciclo de parada a otro, ya que la gente se mueve y cambia de rol
El alcance puede haber sido poco definido en los cronogramas de paradas anteriores
No se incluyeron actualizaciones de progreso precisas y las duraciones planificadas vs. reales podrían haber sido diferentes, pero esto no se registró
Nuevo alcance, nuevos equipos, nuevos métodos de trabajo, etc., cambian la película
Cuando esto sucede, a los planificadores solo les queda su experiencia y la información de referencia que pueden encontrar de trabajos similares realizados en otras unidades o plantas o de referencias de la empresa/industria. Y esto es mucho trabajo.
¿Por qué? Muy sencillo, primero hay que entender la naturaleza del trabajo que se va a realizar y luego buscar trabajos similares en otras fuentes. Tratar de encontrar un alcance similar en los cronogramas de paradas anteriores en P6 o MSP es como buscar una aguja en un pajar. Es posible que se encuentre cierta información relevante aquí y allá que luego deba ser cosida.
Incluso utilizando referencias de la empresa/industria, tablas de rendimientos, etc., puede que estos no sean precisos. Las típicas tablas de productividad por tamaño y clasificación de brida, o por tipo de intercambiador de calor, etc., pueden ser inexactas por los siguientes motivos:
¿Con qué datos se crearon?
¿Cuándo se actualizaron por última vez?
¿Esos datos son relevantes para la planta donde se realizarán los trabajos?
¿Son precisos para el contratista que realizará el trabajo?
¿Es una comparación de igual a igual?
Estas referencias sirven para desarrollar un cronograma preliminar que debe ser discutido con el equipo de ejecución para su viabilidad. Todo esto hace que lleve mucho tiempo desarrollar el cronograma de una parada de cierta envergadura. Por eso, idealmente, este trabajo debería comenzar 18 meses antes de la parada. La planificación de paradas es una actividad difícil y compleja que a día de hoy lleva mucho tiempo pero creemos que esto puede cambiar radicalmente en los próximos años.
Si algo hace bien la tecnología de inteligencia artificial (IA) es sacar provecho de grandes bases de datos sin estructurar o desconectados. Y si algo se hace en una parada es generar grandes cantidades de datos. En Frontline, hemos desarrollado tecnologías basadas en IA para acelerar el proceso de creación y desarrollo de cronogramas. Conceptualmente, es relativamente sencillo. Nuestra IA hace lo que los planificadores hacen hoy, pero a una escala de 10000x.
Los algoritmos de IA son capaces de entender las actividades a partir de texto natural para luego agruparlas y ordenarlas. Esto es exactamente lo que necesitan los planificadores, pues les permite tener un repositorio en vivo de datos de productividad de proyectos anteriores en cuestión de segundos. No solo eso, si el planificador introduce el alcance de alto nivel del evento de parada futuro, la IA puede:
Generar un cronograma detallado con un desglose de actividades y duraciones basado en los datos de paradas anteriores y el plan actual
Resaltar las diferencias significativas entre el alcance de las paradas anteriores y el plan actual, para que el planificador lo compruebe
Servir como un chat-GPT que explique el porqué y los datos detrás de la definición de la actividad
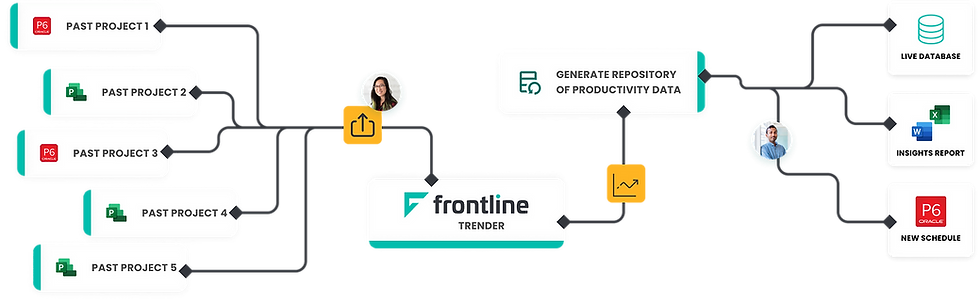
Varios de nuestros clientes han probado con éxito la tecnología de IA que hemos desarrollado. La reducción del tiempo necesario para desarrollar un cronograma pasa de 2-3 meses a 1-2 semanas. ¿Por qué? Se elimina la mayor parte del trabajo repetitivo, de "copiar y pegar", y los planificadores solo necesitan centrarse en lo que aporta mayor valor añadido: definir las partes poco claras, desafiantes y complejas del alcance, donde su experiencia marca la diferencia.
Esta publicación ha tratado la fase de desarrollo del cronograma para un evento de parada futuro. Suscríbete a nuestro blog para la siguiente publicación sobre la siguiente fase: optimización del plan de parada.
Comentarios